KW 7-post driving dynamics test
The KW test center in Fichtenberg provides motor sport teams and industry partners the ability to simulate suspension travel of the vehicle on actual race tracks. This is done KW's hydraulic 7-post driving dynamics test rig.
Whether using 4post sweep, 4post track replay or 7post track replay. The KW test center allows motor sport teams the ability to read between 50 to 100 measurements per day depending on the type of racecar. Setting up a KW competition damper systems will prove beneficial as you'll be able to maximize the added benefits of the competition damper system.
During the test cycle, the KW Competition suspensions can be removed and immediately adapted to the results by the KW Race Service personnel. Testing on the 7 post rig provides the added benefits of no wear and tear on the vehicle, no race track fees/expenses and reduced testing times. The test rig with its various test options is of high interest for race teams that participate in touring car racing, LMP1, LMP2, DTM, ADAC GT Masters, WTCC or also in Rally racing. The test rig has been a mainstay of many Formula 1 teams racing programs for many years. The KW test center is frequented by many Formula type race teams throughout the year.
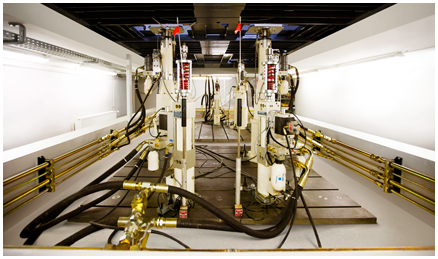
Post mode by vehicle class
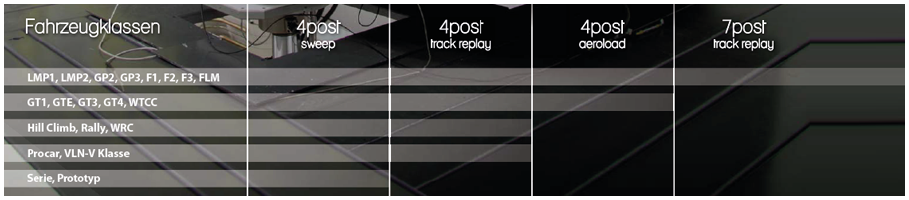

Advantages
The 7post driving dynamics test rig owned by KW automotive offers customers the ability to perform an analysis and optimization of the vertical dynamics of their vehicle.
Advantages
- Repeatability due to consistent external environmental conditions
- objectivity
- Saves time (50-100 measurements per day / depending on vehicle type)
- No wear and tear on the vehicle
- No track rental
- Tests of vehicles possible that are not ready to drive
- Continuous documentation of all measurements
- Data analysis with Matlab® and MS Excel®
- Optimization of different parameters
- Body movement
- Construction frequencies
- Wheel load variations
- Minimum tire contact forces
- Dynamic vehicle level
- Attenuation
- Anti sway bar tests
- Influence of different types of tires and - pressures
- Determination of dynamic tire stiffness
- At KW dampers, a change of damper assembly & spring choice is directly possible. The characteristic curve of dampers can be adjusted.
Infrastructure & Confidentiality
Test rig and workshop are located in separate buildings. Loading and unloading the vehicle inside building is possible (max. transporter height 3,2 m). Secure electronic locking system with access rights.
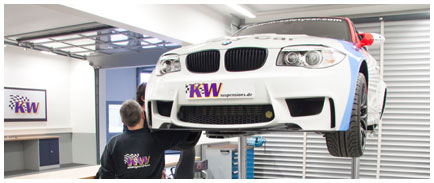
In addition to the test rig, a workshop area with a vehicle 2-post lift are available. Furthermore testing possibilities on damper tests from the companies Schenk (crank mechanism), API Dyno (electronic-mechanical) and Röhrig (hydraulic) are available.
- Ballast dummy: 75kg/165 lbs
- Ballast wights: 50 x 12kg/26.5 lbs
- Additional weights available.
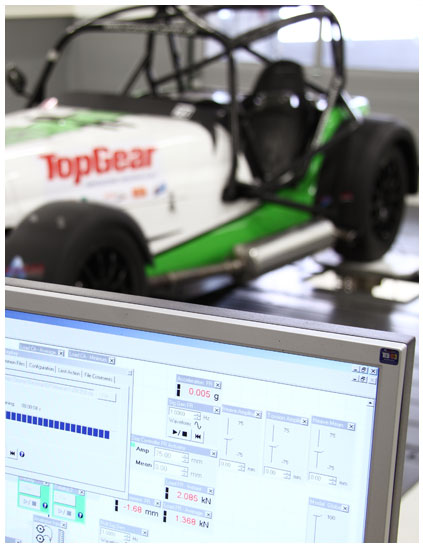
Vehicle requirements
- wheelbase: min. 1100 mm / max. 4200 mm
- tracks: min. 600 mm / max. 1900 mm
- weight: max. 3,5 per vehicle
Current state of vehicle
-
weight
- relevant fuel tank capacity
- Engine, gearbox, bearings in the state of use
- Axle measurement values set up
- Vehicle height
- Relevant tires dry / wet with air pressure data
- Axles, at least camber adjusted, vehicle height adjusting to drive
- At customer-specific sensors to matching adapter on LEMO connector type
- If available, bring spare springs and shocks absorbers
- Lifting station with air bottle ready
- Bring rim lock or tool for central locking

The analysis methods
4post sweep analysis
Test procedure
Frequency sweep with constant stimulation rate of 50, 100, 150, 200 or 250 mm/s and increasing frequency of 1- 20 Hz or frequency and speed according to the customers request
- Optimization of the body movement (balance)
- Optimization of the body frequencies (purpose)
- Optimization of the wheel load variation, RMS divides into low frequency [2-6Hz] and high frequency [6-18Hz] range (traction)
- Optimization of the minimum wheel contact force (traction)
- Optimization of the dynamic vehicle level (compression / rebound relation)
- Optimization of the damping ration via the complete sweep (Ratio between spring - and damping forces)
- 4 wheel acceleration sensors
- 2 body acceleration sensors
- 4 way sensors on the shock absorbers
Optimization of body movement / pitch
Purpose: Keep phase shifting between the front and rear body acceleration during the entire frequency range as low as possible. The example shows an improvement in the relevant range (between 2 and 6 Hz).
Pitch - graph before and after optimization
Optimization of dynamic vehicle niveau / Jacking
Purpose: The balance between in and out of suspension travel. This can be reached with the right compression / rebound relation.
Spring travel before and after optimization
Optimizing of the damping ratio
Purpose: The balance between spring forces and damper forces.
Development of damping factor for front and rear axle during an optimization process
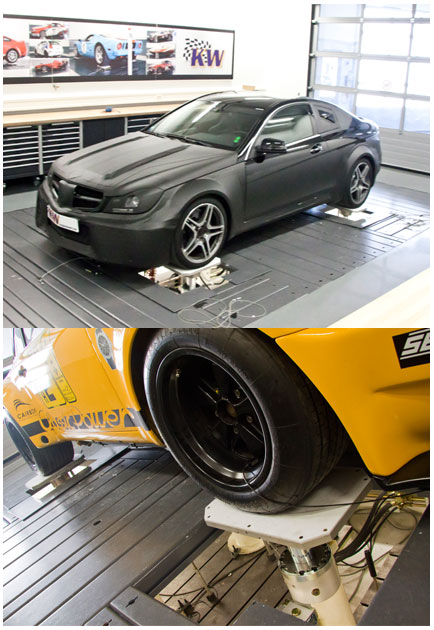
Optimization of wheel load variation
Purpose: to reduce wheel load variations in the low frequency and high frequency range.
Wheel load variations in low and high frequency range before and after optimization
Optimization of the minimum wheel contact force
Purpose: To maintain the minimum wheel contact force on the highest possible value.
Wheel load variations in low and high frequency range before and after optimization
4post track replay (aeroload)
Test procedure
Stimulation of the actuators via a drive file that was created by track iteration from real track data. The analysis is made trac-specific, global and sector-wise
- Data processing and iteration of the track data to create the drive file on the test rig
- Definition of track sectors with problem areas for a differentiated evaluation at different driving conditions
- Dividing options: braking, cornering, traction and notch sectors and low-, middle- and high-speed sectors
- Track sectoral optimization of wheel load variations
- Track related optimization of the body frequencies
- Track sectoral optimization of the dynamic vehicle level
- Optional: Implementation of a 4-post analysis
Additional requirements
- Track data for the measured vehicle must be present
-
Mounting of acceleration sensors on the wheel carriers and linear
potentiometers for recording the spring means
- above mentioned sensors to record the track data are rented
-
In addition to the vertical hub acceleration, the following channels are recorded in the data recording:
- Longitudinal acceleration
- Lateral acceleration
- Throttle position
- Driving speed
- Brake pressure
- Steering wheel angle
Track sectoral optimization of body accelerations
Purpose: Reduction of body accelerations, global and sector-wise.
The graphs show an excerpt from the course of the optimization process.
Sector definition
- Track specific sector classification based on customer-defined
- data recording
- Dividing in braking, cornering, traction and notch sectors
- Problem detection in fix defined segments
Sector definition at the example Hungaroring - Budapest
Route sectorial optimization of wheel load variation
Purpose: Reduction of body accelerations, global and sector-wise.
The graphs show an excerpt from the course of the optimization process.
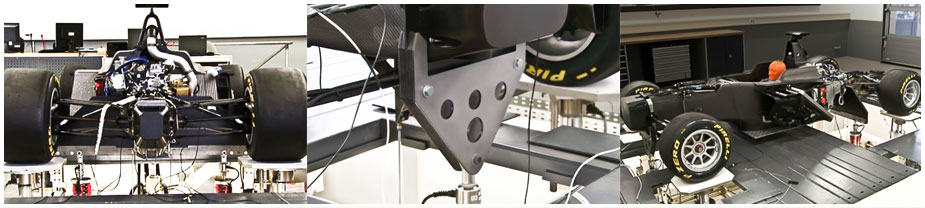
7post track replay
Test procedure
In addition to operating the 4 wheel post, additional 3 actuators are used to simulate real driving forces. Excitation of the actuators via a drive file that was created with track iteration from real track data and a aeromap. The analysis is made track specific, global and sector-wise.
Services / Analysis
-
Data processing and iteration of the track data to create the drive file on the test rig
-
Simulation of aerodynamic loads according to specification or aeromap
- Definition of track sectors with problem areas for a differentiated evaluation at different driving conditions
- Dividing options: braking, cornering, traction and notch sectors and low-, middle- and high-speed sectors and definition of under and over steering
-
Track sectoral optimization of wheel load variations
- Track related optimization of the body frequencies
- Track sectoral optimization of the dynamic vehicle level (ride height)
- Implementation of real rolling moments
- Optional: Operation of a 7post sweep - Analysis
Additional requirements
- Data for aerodynamic must be present
- Position of the vehicle center of gravity must be known
- Track data for the measured vehicle must be present
-
Track data for the measured vehicle must be present
-
above mentioned sensors to record the track data are rented
-
in addition to the vertical hub acceleration, the following channels
are recorded in the data recording:
- Longitudinal acceleration
- Lateral acceleration
- Throttle position
- Driving speed
- Brake pressure
- Steering wheel angle
- Brackets for aero actuators / LVTs
Further analysis methods
All analyses of the 4post track replay analysis mode can also be used in 7post track replay without any problems.
Test procedure
In addition to operating the 4 wheel post, additional 3 actuators are used to simulate real driving forces. Excitation of the actuators via a drive file that was created with track iteration from real track data and a aeromap. The analysis is made track specific, global and sector-wise.
- Data processing and iteration of the track data to create the drive file on the test rig
- Simulation of aerodynamic loads according to specification or aeromap
- Definition of track sectors with problem areas for a differentiated evaluation at different driving conditions
- Dividing options: braking, cornering, traction and notch sectors and low-, middle- and high-speed sectors and definition of under and over steering
- Track sectoral optimization of wheel load variations
- Track related optimization of the body frequencies
- Track sectoral optimization of the dynamic vehicle level (ride height)
- Implementation of real rolling moments
- Optional: Operation of a 7post sweep - Analysis
- Data for aerodynamic must be present
- Position of the vehicle center of gravity must be known
- Track data for the measured vehicle must be present
-
Track data for the measured vehicle must be present
- above mentioned sensors to record the track data are rented
-
in addition to the vertical hub acceleration, the following channels
are recorded in the data recording:- Longitudinal acceleration
- Lateral acceleration
- Throttle position
- Driving speed
- Brake pressure
- Steering wheel angle
- Brackets for aero actuators / LVTs
Further analysis methods
All analyses of the 4post track replay analysis mode can also be used in 7post track replay without any problems.
Aeromap
Graphic representation and analysis of the front or rear output coefficient and the aero balance depending on the vehicle level during the test procedure.
Ride height optimization
- Analysis of the approached ride height in the aeromap
- Determination of the ideal ride height in the single track sectors
- Comparison of various aero maps and determination of the corresponding optimal ride height
Analysis of the stabilizer stiffnesses
Purpose: To evaluate the effects of different stability configurations.
Processing of stabilizer influence on the wheel load of front and rear axle

Range of service overview
1. 4post rig sweep analysis & track replay (aeroload)
Article |
Description |
Extent |
|
1.1 |
Preparation and set up - 4post - |
Set up post mount sensorsn calibrate max. 3 hours |
|
1.2 |
Test rig use - 4post - |
Vehicle
|
Servo test rig incl. engineer
4 actuators 4 linear potentionmeter 4 sensors / hubs acceleration 2 sensors / body acceleration Workshop with 2 post lifts Packag for 1 day (8 hours) |
1.3 |
Test rig use - 4post track replay - |
Track- and sector-specific measurements:
and total round |
Servo test rig incl. Engineer
Preparation of data record, iteration of a track 4 actuators 4 linear potentionmeter 4 sensors / hubs acceleration 2 sensors / body acceleration Workshop with 2 post lifts Packag for 1 day (8 hours) |
1.4 |
Test rig use - 4post track replay with constant Aero-Loads - |
Track- and sector-specific measurements:
and total round |
Servo test rig incl. Engineer
Preparation of data record, iteration of a track 4 actuators 4 linear potentionmeter 4 sensors / hubs acceleration 2 sensors / body acceleration Workshop with 2 post lifts Packag for 1 day (8 hours) |
2. 7post rig track replay (optional: sweep analysis)
Article |
Description |
Extent |
|
2.1 |
Preparation and set up - 7post - |
Set up post, bracket mounting
mount sensors, mount vehicle on test rig, calibrate max. 5 hours |
|
2.2 |
Test rig use - 7post track replay - |
Track- and sector-specific
measurements:
and total round |
Servo test rig incl. engineer
Preparation of data record, iteration of a track, sector classification 7 actuators 4 linear potentionmeter 4 sensors / hubs acceleration 2 sensors / body acceleration Workshop with 2 post lifts Packag for 1 day (8 hours) |
3. Extras
Article |
Description |
Extent |
|
3.1 |
Iteration |
Iteration track or load collective |
at expenditure / hourly rate |
3.2 |
Additional engineer |
Support analysis on the test rig or when creating the data at the track |
Package for 1 day (8 hours) |
3.3 |
Mechanics working hours |
Support, test rig work, change of settings, Installation / deinstallation damper & springs |
Package for 1 day (8 hours) |
3.4 |
Rent sensor package I/div> |
Hardware for data recording |
4 linear potentiometer
4 sensors wheel acceleration 2D Package for max. 7 days / additional day |
3.5 |
Rent sensor package II |
Hardware for data recording |
4 linear potentiometer
4 sensors wheel acceleration ATEX Package for max. 7 days / each additional day (incl. installation and transportation time) |

KW 7post catalog - Download
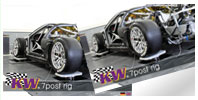
You would like to save all the information on this page as download? Please click on the link or the PDF icon to load our 7post catalog.
Contact - driving dynamics test
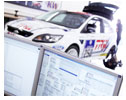
Klaus Frank, Manager 7post rig / damper development
Dipl.-Ing. Cäcilia Fromme, Rig Engineer
Phone: +49 (0) 7971 / 9630-0